The 3p fastening system and its elements
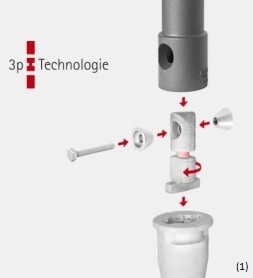
The junction piece with pre-determined breaking point will not suffice on its own to ensure the 3p-Technology functions as required. While it is the central element of the fastening system, the overall user-friendliness is also the result of some additional parts. Only by smoothly interlocking the individual components can the variable, adjustable fastening system be achieved.
It consists of a ground shell anchored into the ground, a replaceable junction piece with pre-determined breaking point, a clamping cone set for fastening, and of course the bollard or other compatible product. If damaged, e.g. by a car, the bollard does not fully bend over or break off; only the junction piece with pre-determined breaking point breaks. This is easily removed and replaced with a new junction piece. The time and
expense involved here is minimal compared to conventional bollards and barriers.
Ground shells and covers
Bollard sturdiness of course takes top priority, as evidenced by the various types of ground shells. Depending on design, the ground shells weigh between 5 and 8.6 kg. They can also be adapted to any subsurface to ensure optimum hold.
- The 300 mm ground shell is the standard format.
- If the subsurface is not paved or if it has high paving stones, such as cobbles, the 500 mm ground shell is better, as it provides greater stability. To ensure only the junction piece breaks, it is crucial for the concrete foundation to be flawless.
- The 100 mm ground shell, on the other hand, is a special shape designed to be affixed in places with shallow installation depths. It is therefore ideal for parking buildings, bridges or similar.
While the assembly instructions stipulate a rectangular ground shell, many customers use normal core drill holes, which, experience has shown, are adequate for most sub-surfaces. It’s important to ensure the ground shell area is angular and doesn’t have rounded edges.
Junction pieces
The junction pieces form the central element of the 3p-Technology, as they connect the bollard to the ground shell. They are particularly distinguished by their integrated pre-determined breaking point, which serves as the basis for
the 3p system’s cost effectiveness. Just like the screws and ground shells, ABES also offers different versions of the junction pieces, ensuring the best possible solution for any purpose.
This is largely due to the modular nature of the individual parts, making them almost infinitely compatible with one another.
They can also be re-ordered without any problem, meaning things like standard hexagonal screws can be replaced with less easily removed screws. The same applies to all clamping bolts and junction pieces.
ABES – The 3p-Technology
The junction pieces for the 3p fastening system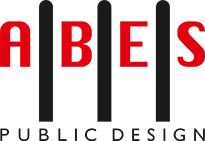
-
Junction piece with pre-determined breaking point
The
standard version commonly used in products with 3p-Technology.
Material: Cast iron, hot-dip galvanised
-
Junction piece without pre-determined breaking point
The design
without a pre-determined breaking point gives the bollard mode stability, though it can mean the bollard suffers more serious damage if hit.
Material: Cast iron, hot-dip galvanised
-
Junction piece with anti-roll stop
This version
prevents the bollard from rolling away after impact thanks to a solid steel rod running through the Junction piece and pre-determined breaking point.
Material: Cast iron, hot-dip galvanised
The ABES Junction pieces made from special cast iron with steel-like properties only exist in two states – they are either intact or broken. They cannot be bent or twisted.
- Junction piece with pre-determined breaking point: The standard version commonly used in products with 3p-Technology.
- Junction piece with anti-roll stop: This alternative has a steel rod running through the Junction piece and pre-determined breaking point. While this does not prevent the Junction piece from breaking, the bending of the steel rod - the bending degree depends on the incoming force caused by the mass and speed of the crashing vehicle - does ensure the bollard cannot roll away. This solution is particularly useful in places with heavy traffic flows (i.e. in inner cities), on sloping streets, or anywhere a broken bollard could pose a hazard to people, vehicles or buildings (particularly those with large window displays). Standard Junction piece designs can also be changed to anti-roll stops later on.
- Junction piece without pre-determined breaking point: The version without a pre-determined breaking point is a bollard featuring 3p-Technology which, on the one hand, has the robustness of a permanent fitting, while still providing the option of being removed. The lack of pre-determined breaking point means the bollard does not buckle when hit, though this can cause damage, as it affects not only the Junction piece, but also the entire bollard, together with foundations and possibly even paving stones. These Junction pieces are ideal in places where the safety of people and buildings take precedence over costs and damage, such as narrow lane-ways or public squares. Multiple rows of barriers containing Junction pieces without pre-determined breaking points may well be enough to critically slow down a dangerous vehicle or, in the best case scenario, even bring it to a halt.
The 3p-Technology offers a number of advantages here: On days where there is no heightened security risk, additional bollards can be easily removed and the ground shells closed
with appropriate covers. If, however, there are expected to be large events with big crowds (such as concerts, fun fairs or Christmas markets), and therefore a higher security risk, extra protection can be quickly and easily provided in the form of additional rows of barriers.
This is also a comparatively low-cost solution. In cases of doubt, the bollards can be set up and dismantled very quickly, without disrupting the overall look of the scene, as is the case with concrete blocks. Droplet screws can also be used as additional security measures to make the bollards much more difficult to remove illegally.
Screws
When it comes to
the screws used in the 3p fastening system, customers can choose from various products which can be tailored to location and purpose:
- Standard hexagonal M12 screw: This is the screw used in all conventional ABES clamping cone sets. As with all screws, the rolled screw thread is made from stainless steel, and measures 75 mm in length.
- Triangular M12 screw (as per DIN 22417): Triangular screws are generally used in places where the fire brigade, police or rescue services must be able to access private roads and areas with their vehicles. In addition to these triangular screws, ABES also offers matching accessories, such as the “standard’ or “robust” screws and triangular nuts available upon request.
- ABES special “droplet” screw: This version has been developed and registered for a utility model by ABES. It may only be unscrewed using a special tool. It also only permits certain people from removing the bollard, as this is virtually impossible without the special tool.
Clamping bolts
Clamping cones are used to connect the bollards with the ground shells. They also prevent bollards and barriers from having too much give, ensuring they remain sturdy and stable. All available versions are made from stainless steel, and may be used for all products containing the 3p-Technology.
In addition to the security measures guaranteed by
the various screw heads, the clamping cone set with
extended clamping cone can also be secured by a padlock. This double protection makes it even harder to illegally remove the bollards.
Tools
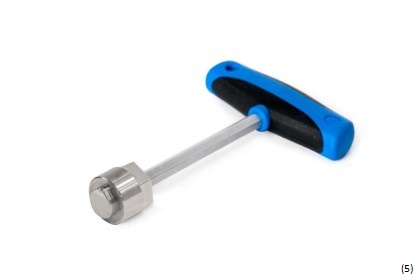
ABES of course also provides
the tool to go with the screws. In addition to the standard triangular screws, highly robust socket wrenches are also available for the
special ABES bolt - Teardrop shaped - and triangular screw. These special tools are made from twisted, machined stainless steel, and have an ergonomic plastic handle, guaranteeing fast, easy screwing and unscrewing.
The tools specially designed for droplet and triangular screws – socket wrenches and ratchet nuts – are also distinguished by their outstanding firmness and stability. ABES similarly offers the specific nuts required for all special screw-head shapes.
3-pin socket wrenches
The little holes in the N2 clamping cone are a unique feature, and are a perfect fit for the
3-pin socket wrench. This wrench is used to lock (not tighten or loosen!) the clamping cone in the event the clamping cones rotate during loosening after several years or after road salt has been used. Having the N2 clamping cone locked – i.e. held in place – enables the entire system to be opened with relative ease.
Fastening options to suit all needs
ABES offers a wide range of street furniture, from
bollards and barriers to
park benches, tables,
bins and
bicycle stands. For some of these products, the 3p-Technology originally developed for the barriers has been adapted to enable bench systems and bins to also be assembled using the easy, modular system. The various fastening options also guarantee customised assembly, fully tailored to customer requests and requirements.
3p-Technology and 3p-High
Fitting the fastening systems generally always follows virtually the
same process (pdf):
- Step 1 involves digging a hole for the foundations. NB: Round shapes in the ground shell area must be avoided at all costs. The dimensions should be chosen depending on the ground properties (but the depth is usually between 50 and 70 cm, and width and length approx. 50 cm x 50 cm), and it is important to also ensure the foundations have a water drain. The ground shell is then laid flush to the ground and positioned horizontally. The notches indicate how the ground shell surfaces can simply be arranged in a line (see assembly instructions).
- Step 2 involves placing the Junction piece into the ground shell, then turning it 90° (NB: There is no stop in the ground shell!).
- Step 3 consists of assembling the bollard, which is placed onto the Junction piece in such a way that the holes in both elements sit on top of one another.
- Finally, step 4 sees the bollard affixed using the clamping cone set.
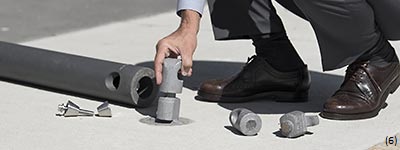
As the ground shell 100 is fastened without a ground shell, it is first important to ensure a firm, even subsurface. Four drill holes are also required for stud bolts. The upper edge of the ground shell anchored onto the subsurface can either be concrete-cast, paved in or bitumen-cast. It should be flush with the ground where possible. Otherwise,
the bollard is set up and fastened as described above.
In the “3p high” variant, the screw joint is set higher up the bollard than on standard versions. It is primarily intended to be used with a long-handle triangular screw. This provides more room below for the tool’s lever strokes, enabling the screw joint to be opened and closed without moving the tool. This can significantly speed up the bollard removal process, especially during fire-brigade and rescue-service call-outs, when time is a critical factor.
ABES – The 3p-Technology
The junction pieces for the 3p fastening system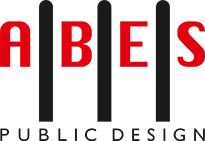
-
Extended Junction piece (3p high)
The
extended Junction piece means the locking device is higher up the bollard. This particularly makes it easier for the fire brigade and other rescue workers to open and close it with long-handle triangular screws.
Material: Cast iron, hot-dip galvanised
Permanent installation, screwing on, and removing
The removable bollards also give you the option of taking them out of the ground shell without separating the individual parts. The clamping cone set should not be fully loosened here, but rather only to the point where it becomes noticeably loose. Turning the bollard 90° enables it to be lifted out, together with its Junction piece. Re-fitting it follows this same process in reverse order.
Although the benefit of 3p-Technology is having
lower costs in the event of damage compared to a permanent installation without 3p-Technology, you also have the option of concrete-casting the ABES bollards and barriers. The Junction piece is not necessary here, meaning the bollard can no longer be removed. This also applies to the bollard versions screwed into the subsurface.
One system, lots of options
The 3p-Technology is not only practical and cost-effective; its modular nature also makes it extremely flexible. As all components are available in different but compatible designs, the fastening system can be fully tailored to specific needs, requirements and conditions. It is important to remember here that the
3p-Technology can help boost security and safety in public spaces – for a comparatively moderate cost.
NB: Due to the unpredictability of everyday traffic, the aforementioned properties cannot be guaranteed. The products have been carefully developed for hard everyday use, and are thus suitably robust.